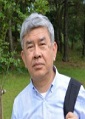
Kunihiko Furuzaw
GMP Consultant, Japan
Title: Risk base Technical transfer in pharmaceutical manufacturing
Biography
Biography: Kunihiko Furuzaw
Abstract
Technical Transfer of processes to an alternative site occurs at some stage in the life-cycle of most drug substance/products, from development, scale-up, manufacturing, production and launch, to the post-approval phase.
Technical transfer is defined as “a logical procedure that controls the transfer of any process together with its documentation and professional expertise between development and manufacture or between manufacture sites” as one part of Change control. It is a systematic procedure that is followed in order to pass the documented knowledge and experience gained during development, and or commercialization to an appropriate, responsible and authorized party.
Technology transfer embodies both the transfer of documentation and the demonstrated ability/capability of the receiving party(ies) to effectively perform the critical elements of the transferred technology, to the satisfaction of all parties and any applicable regulatory bodies.
Technical Transfer requires a documented, planned approach using trained and knowledgeable personnel working within a quality system, with documentation of data including of risk assessment/ mitigation covering all aspects of development, production, quality assurance and quality control.
For the transfer to be successful, the following general principles and requirements should be met:
1) the project plan should be based upon the principles of quality risk management, 2) the capabilities of the providing and at the receiving party should be similar, 3) a comprehensive technical gap analysis, technical risk assessment and potential regulatory gaps, should be performed as needed, 4) adequately trained staff, 5) effective process and product knowledge transfer.